A Short Primer On The Power Transformer Industry
May 13, 2020
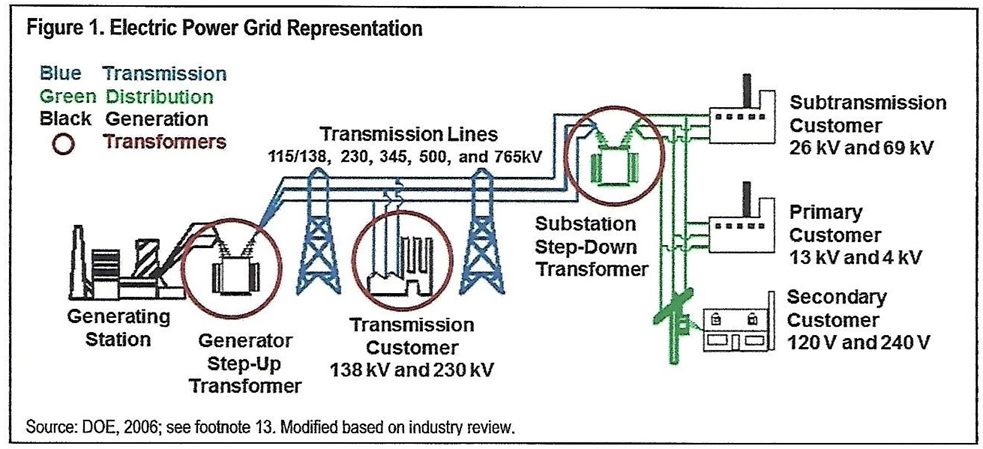
The large transformer industry for electricity supply and distribution consists of two main parts: a) Power Transformers, which handle high voltage power typically from generation to a central source of distribution, or sub-station. This is typically known as “the grid”. And b) Distribution Transformers, which handle the distribution of lower voltage power from central points to points of actual usage, such as the pole mount transformers that supply power to our houses.
Both Power and Distribution transformers handle “power” in terms of voltage and current. To the uninitiated, the general term “power”, otherwise “energy” is confused with or interchanged/added to the description of Distribution transformers, which indeed handle power.
There are 2 main types of imported cores: a) imported cores for power transformers consist of big assemblies , typically with 3 “legs” and perhaps a minimum or 5 ft high, usually bigger, and b) imported cores for distribution transformers (where the current battle ground is).
Imports of power transformer core assembly units are relatively low because they are very labor intensive. It is much more usual for the Power Transformer manufacturers to assemble these cores in house using special equipment to slit and cut the many specialized dimensions required for the “round” assemblies on each leg.
Imports of distribution transformer cores in another matter. There is a whole competitive industry devoted to buying steel, slitting it to width and then cutting individual lengths which go into the two halves of a core. Quick and simple. However, there is sophisticated computer equipment used to control cutting of the lengths that go into making the core. The HUGE advantage of the core is 2-fold. Firstly, the industry uses international lower priced grain oriented steel (GOES) and also uses the lower grades, that sell for lower prices (because distribution transformers do not require the best grades of GOES which go into power transformers). Second, the core can be split apart and put back together, which allows transformer manufacturers to make copper coils separately, on automated equipment, not hand wound, and insert them into the split apart grain oriented steel cores. The cores are more correctly called Distributed Gap Cores because the computer cutting distributes the gap inside the core for improved efficiency. Thus, the distribution transformer business becomes a job-shop where cores are commodities that can be purchased quickly, copper coils are made on site in the USA to specification (and to orders as low as one) and tanks, insulators, oil, etc are all commodities. The big cost is the material used for the steel core. The irony (pun intended) is that AK Steel specializes in the high grades of grain oriented electrical steel. Properties are great but prices are usually much higher than other offerings in the marketplace. The biggest volume of imported cores uses lower grades where AK Steel would like transformer manufacturers to use its higher grade steels. Better efficiency but uncompetitive prices for the transformer manufacturer. AK Steel is between a grain oriented Rock and a Hard transformer place, thus the request for protection under the Section 232 banner.
There are other types of cores. Laminations are typically stamped or cut to length and represent the much smaller part of the market and industry. The term laminations is primarily added to the description such that it becomes “all inclusive”.
0 Comments